Business’s inventory
- 549576
- Nov 18, 2021
- 3 min read

Accounting for merchandise inventory is generally easier than accounting for manufacturing inventory. The reason for that it's because a merchandising company, such as a retail store, has only one class of inventory to keep track of: goods the business purchases from various manufacturers for resale.
Here’s an example of the basic flow of inventory for a retailer: A linen sales associate at a major department store tells the manager that a certain style of linen is in low supply. The manager follows the store’s purchasing process, and the store receives a shipment of linens from its vendor.
This transaction is a purchase (cost), but it’s not an expense until the department store sells the linens. So the business records the entire shipment of linens on the balance sheet as an addition to both inventory and accounts payable. Accounts payable is used instead of cash because the department store has payment terms with this vendor and money has yet to change hands during this transaction.
Say that in November, the store sells linens to customers for $150 that cost the company $75 to purchase from the vendor. Sales revenue increases by $150, cost of goods sold increases by $75, and inventory decreases by $75. Matching the expense to revenue, the effect to net income is $150 sales – $75 cost of goods sold = $75 profit on sale.
Pretty basic stuff. The company buys inventory and sells it. Next, you consider how retail shops normally track inventory. Two major types of inventory systems exist: perpetual and periodic.
Perpetual system
Most larger retailers have electronic cash registers (ECRs) that scan the bar code of each product and record the sale into the system, along with an increase to cash.
Periodic system
With a periodic system, the physical inventory is taken periodically, and the resulting figure is used to adjust the balance sheet “inventory asset” account. This is the same inventory count and adjustment process you see with the perpetual system. However, the perpetual system updates inventory constantly,whereas the periodic system doesn’t.
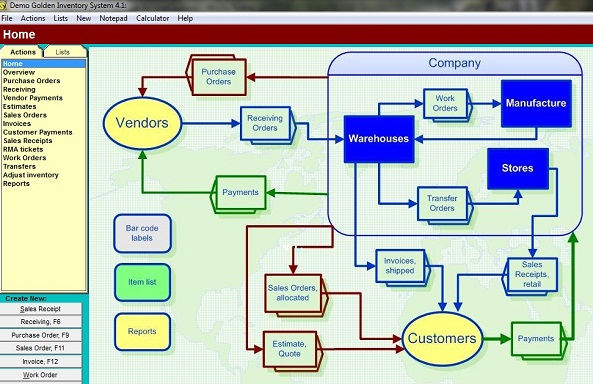
5 Basic types of inventories are raw materials, work-in-progress, finished goods, packing material, and MRO supplies. Inventories are also classified as merchandise and manufacturing inventory. Other such classifications on various bases are goods in transit, buffer stock, anticipatory stock, decoupling inventory, and cycle inventory.
Raw Materials
These are the materials or goods purchased by the manufacturer. The manufacturing process is applied to the raw material to produce desired finished goods. For example, aluminum scrap is used to produce aluminum ingots. Flour is used to produce bread. Finished goods for someone can be raw material for someone. For example, the aluminum ingot can be used as raw material by utensils manufacturer.
Work-In-Progress (WIP)
These are the partly processed raw materials lying on the production floor. They may or may not be saleable. These are also called semi-finished goods. It is unavoidable inventory which will be created in almost any manufacturing business.
Finished Goods
These are the final products after manufacturing process on raw materials. They are sold in the market.
There are two kinds of manufacturing industries. One, where the product is first manufactured and then sold. Second, where the order is received first and then it is manufactured as per specifications. In the first one, it is inevitable to keep finished goods inventory whereas it can be avoided in the second one.
Packing Material
Packing material is the inventory used for packing of goods. It can be primary packing and secondary packing. Primary packing is the packing without which the goods are not usable. Secondary packing is the packing done for convenient transportation of goods.
MRO Goods
MRO stands for maintenance, repair, and operating supplies. They are also called as consumables in various parts of the world. They are like a support function. Maintenance and repairs goods like bearings, lubricating oil, bolt, nuts etc are used in the machinery used for production. Operating supplies mean the stationery etc used for operating the business.
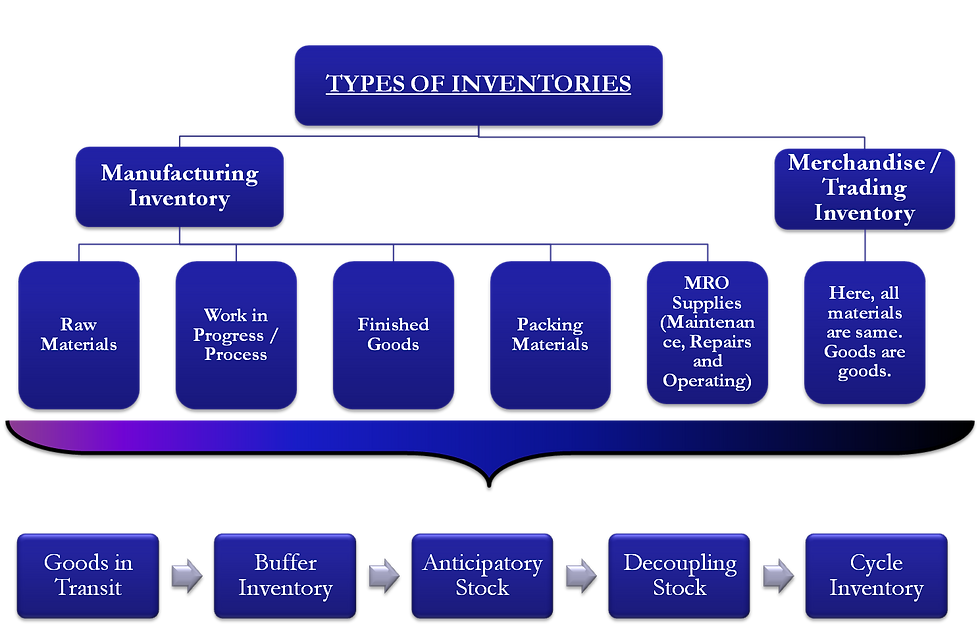
Raw materials is one that We uses the most at Souza's. The inventory refers to all the resources, supplies, and materials required to create or assemble a final product. Managing this inventory is absolutely critical to manufacturers and retailers that assemble some or all of their products.
The successful tracking, stocking, and reordering of so many moving parts require inventory management software with raw materials capabilities. Barcode inventory systems can help manage input, output, and usage of these temperamental inventories, but some items warrant even more specialized inventory systems and protocols, such as storage with vigilant temperature management or limited exposure.
Raw materials are one of a few inventory categories that can be disregarded if you’re a traditional retailer or e-commerce merchant turning products from suppliers to your customers without any assembly. It’s good to have an understanding of the concept given its importance to the industry and your suppliers but it won’t be in your everyday vernacular.

Comments